Станок для лазерной резки труб
Лазерная система резки для обработки металлических труб и профилей
Станок для лазерной резки труб
Лазерная система резки для обработки металлических труб и профилей
Станок для лазерной резки труб предназначен для прецизионной резки труб и профилей, включая швеллеры. Он широко применяется для таких работ, как изготовление труб для фурнитуры, сверление стальных труб, прецизионная резка для печатных применений, гибка и резка профильных квадратных труб, а также резка водопроводных труб для кухни и выхлопных труб автомобилей. Доступные варианты мощности лазера варьируются от 1000 Вт до 30000 Вт, что позволяет настраивать систему в соответствии с конкретными производственными требованиями. Станок обрабатывает трубы диаметром от 20 мм до 460 мм и длиной резки от 3000 мм до 6000 мм, обеспечивая гибкость для проектов различных размеров.
- Особенности
- Технические характеристики
- Примеры
- Компоненты
- Высокоточная резка
Станок для лазерной резки труб использует передовую лазерную технологию в сочетании с высокоточными системами управления движением для достижения непревзойденной точности резки. - Лучшее качество края
Сложные алгоритмы управления станком и функции формирования луча обеспечивают чистые, гладкие края с минимальными заусенцами, что повышает общее качество готовой продукции. - Высокая повторяемость
Станок для лазерной резки труб оснащен современными системами позиционирования и обратной связи, которые гарантируют точную повторяемость параметров резки. - Эксплуатационная гибкость
Настраиваемые параметры, интуитивно понятный пользовательский интерфейс и совместимость с широким спектром материалов позволяют легко справляться с различными задачами резки, оптимизируя производственный процесс. - Простое техническое обслуживание
Благодаря надежным компонентам и интеллектуальным функциям диагностики, станок требует минимального вмешательства для технического обслуживания, что сокращает общее время простоев и обеспечивает максимальную производительность.
Рабочая область | Круглая труба 6500ר640 мм Квадратная труба |
Ход оси X | 6550 мм |
Ход по оси Y | 350 мм |
Ход оси Z | 240 мм |
Точность позиционирования по оси X/Y | ±0.03 мм/м |
Точность перепозиционирования оси X/Y | ±0.02 мм |
Макс. скорость оси X/Y | 80 м/мин |
Точность вращения | ±0.03 мм |
Диаметр трубки | Ø20-460 мм |
Длина трубки | 300-6500 мм |
Макс. вес загрузки | 1500кг |
Вес машины | 9000 кг |
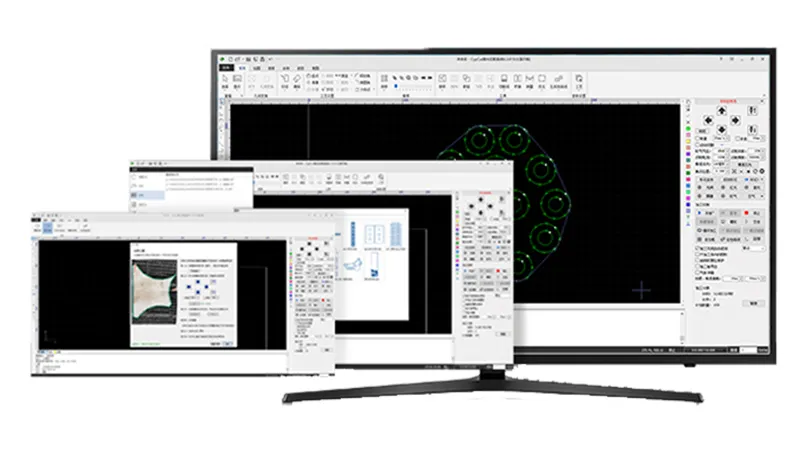
Программное обеспечение Cypcut
- Калибровка давления воздуха: обеспечивает точную регулировку давления воздуха.
- Многоступенчатый пробойник: имеет несколько уровней пробивки.
- Управление энергией лазера: регулирует интенсивность лазерной энергии.
- Адаптивный поиск кромки: автоматически находит кромки реза.
- Функция прыжка: перемещается между различными позициями.
- Автоматическое разгон и торможение в углах: автоматически ускоряется или замедляется в углах.
- Резка на лету: обеспечивает плавную резку без остановки.
- Механическая компенсация точности: точно регулирует механические погрешности.
Дополнительные функции
Лазерный генератор
Лазерная головка
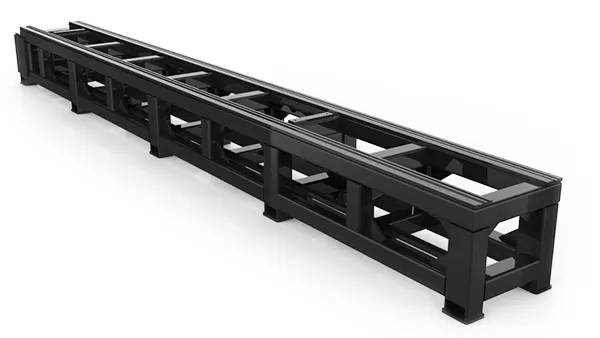
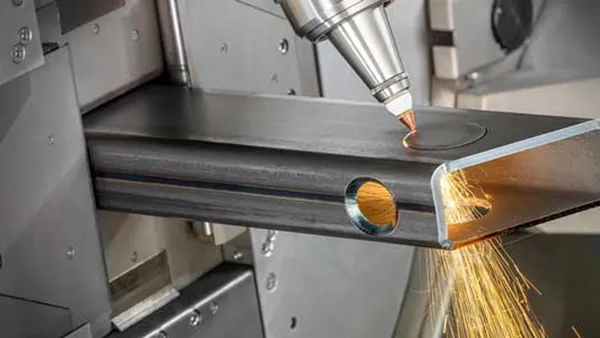
Процесс производства станков для лазерной резки труб компании RZMT
- Каждый станок проходит тщательную сварку и соединение для повышения структурной целостности и долговечности.
- К каждому сваренному из стальных пластин станку применяется высокотемпературная термообработка для снятия напряжения, гарантируя долгосрочную стабильность.
- После отжига станки проходят прецизионную обработку на фрезерном станке с порталом для обеспечения оптимальных рабочих характеристик.
- Внедрены строгие меры контроля качества для поддержания стабильности во время длительной эксплуатации, гарантируя постоянную производительность.
- Строгое соблюдение стандартов установки обеспечивает точную юстировку и фиксацию каждого винта, предотвращая отклонения.
- Точность имеет первостепенное значение: каждая точка винтовой рейки соединяется с двумя рейками для контроля точности позиционирования в пределах 0,01 мм.
- Погрешности вертикальной точности по оси X и Y тщательно контролируются с допуском 0,01 мм.
- После установки и отладки оборудование проходит вторичную калибровку и компенсацию погрешности с помощью лазерных интерферометров.
- Перед отправкой каждый станок проходит 72-часовое испытание на работоспособность и комплексную проверку качества и надежности.